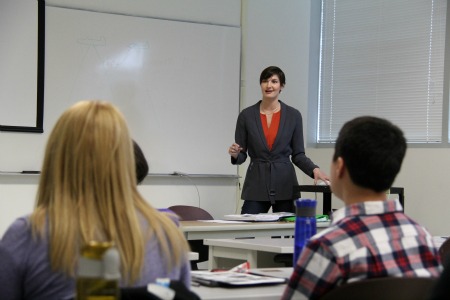
Geoenvironmental engineering PhD student Neeltje Slingerland, seen here teaching a senior geomechanics course, is bringing her background as a landscape architect to her approach to planning for the mining industry.
(Edmonton) There's no sugar-coating the description of a mine site - terms like "wasteland" and "moonscape" are often invoked. But that's the nature of industrial operations. What matters most is what happens to mines after they close. What will they look like centuries or millennia from now?
When geoenvironmental engineering student Neeltje Slingerland visits mining sites, she sees something most people don't: potential.
Slingerland first developed this perspective while studying Earth Sciences at the University of Waterloo. As part of her studies, she and fellow students visited working and closed mine sites, climbing waste rock piles and examining rock samples. She pursued this potential through a master's degree in landscape architecture focusing on adaptive reuse of post-mining environments.
"There are communities all across southern Ontario with mines just out of town. There are literally 100-metre rock walls and a pit and maybe a five-foot-tall fence around it," she says.
"The mining company created a blank canvas by getting rid of everything that was once there. And to a designer-you get giddy over it and start to wonder what could be done with this space."
Slingerland completed her M.L.A. and worked as a landscape architect for a time, planning large residential neighbourhoods and commercial developments. But her thoughts always returned to the mining industry. She met with companies to talk about what she could do for them and they were intrigued, but career opportunities never developed. She decided then to pursue a PhD in engineering.
The program she is in now, geoenvironmental engineering, is similar to geotechnical engineering but has a sharper focus on hydrogeology, the study of how water moves underground, and geochemistry.
Her motivation for returning to school was partly to take on more challenging work that had a higher degree of difficulty and required more technical knowledge, but Slingerland says she is more interested in the impact of that work, of "a greater good" inherent in rehabilitating sites that are often toxic.
"It feels good-really good-when you walk away from a mine site at the end of the day knowing what it might look like in 20 years, knowing that this is a place that can be converted into something that is healthy again."
It's an ethos that runs through the group of graduate students working under the supervision of environmental engineering professor Ward Wilson, who holds the NSERC Industrial Research Chair in Oil Sands Tailings Geotechnique.
"She has a sense of service, the heart of a servant who wants to contribute to those around her," Wilson says of Slingerland. "This group of students has a lot of that. A lot of them are already professional engineers, or have some professional experience, and that makes them a little different. They all have a vision of a future that can be different, a vision they aspire to."
The 20-year timeframe Slingerland refers to just scratches the surface of the depth of planning she has in mind. She wants oil sands mining companies to look centuries or millennia into the future, knowing that the land they are working on will be a mine for only a brief time, but that geotechnical and geomorphic processes will act on the land over extended timeframes.
Tailings from oil sands operations are in a category of their own because of the length of time it takes for fine particles to settle. A 100-metre mound of pure tailings could take 100 years to settle and during that time its height could reduce to about 80 metres.
"As you can imagine, this has implications when designing a tailings dam for closure, ensuring it still sheds water and functions safely while these changes are occurring and after they've ceased," she said.
"How do you design for 10,000 years into the future?" she asks. "That's what we're trying to do-design with the end in mind. Right from the outset, we should ask ourselves what we want this land to look like after the mine closes. Do we want it to be green rolling hills? Let's design it for that. We should know what the end game looks like and design for that."
Mine sites need to be examined and planned in ever-expanding circles, starting with the mine itself, then the neighbouring land and its occupants and uses, and future possibilities. For example, while working on the prefeasibility closure landform design of a tailings pond for a major oil sands operator over the summer, Slingerland explored the possibility of building a higher berm to add capacity to the pond, while mimicking natural topographic features of the region. The problem was that this approach required a longer slope to support the berm-which would have encroached on property the company doesn't own.
Mine operators need to look carefully at the natural history of the area-from the geological forces that shaped the land, to the impact the mine will have on it, and what it could look like well into the future.
Mining companies are required by legislation to have plans for mine closures. But the approach Slingerland is proposing demands a level of detailed planning that has not yet been employed. Wilson says the difference is that companies today try to restore land formations created by engineers based on economics. "But an architect envisions the final product then thinks about how to build it. She is bringing that forward thinking to the process."
For example, Slingerland says mine plans should even take climate change into account.
"We cannot just mimic landform typology. We need to be asking what the landscape will look like 500 years from now. If climate change means the Boreal forest is moving, then why would you design the land for more of the same? That won't fly."
The economics of the mining industry are such that decommissioning costs are treated separately from design, build and operational budgets-leaving these costs out of the equation until years later makes an operation's numbers look better. But Slingerland is hopeful that the industry will begin to take realistic closure costs into account at the front end of mining operations.
"We keep hearing discussions about "No more tailings dams-this is unacceptable," she says. "The message seems to have gotten through but it's going to take a while to see action. Ideas like this (detailed, long-range planning) have been around, but we need more examples from industry to demonstrate that this isn't a financial liability."
In many cases, decommissioning costs grow because detailed planning takes place toward the end of a mine's life and there are unforeseen costs.
"You don't know everything you're going to need until you act something out," she explains. "If you start with a detailed inventory and analysis and you have that level of detail in your planning, it's easier to know what blanks you're going to have to fill in during implementation-otherwise, it (reclamation) is a discovery process all the way through."